Introduction to an Aircraft Wiring Harness
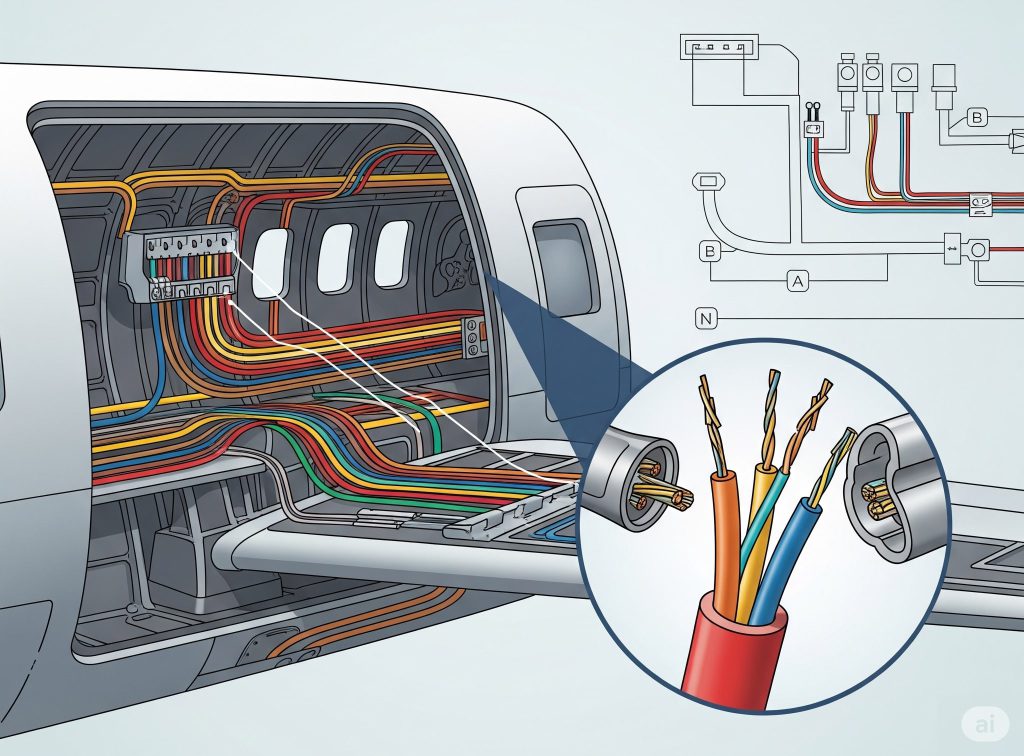
What is an aircraft wiring harness or wire loom? To start with, harnesses are a testament to what man has achieved in science and technology. Although the functionality of this innovation may be considered straightforward and simple, its vast applications and different variations prove how much it has made an impact in the technological revolution.
Wire harnesses are often seen inside many electronic products today and are also the foundation of the car manufacturing industry. However, technological advancements have made it possible to utilize versatile and reinforced wire harnesses that are applicable in other rigorous sectors just like in the aviation or aircraft industry.
THE EVOLUTION OF AIRCRAFT TECHNOLOGY
Getting on a plane in this modern era of technology might sound like an unremarkable act that plenty of us have done in the past. Nonetheless, the history behind aircraft technology has come a long way to get to where it is today. In the early days of aviation, aerodynamics was the center of aerial navigation. Hot air balloons were the first type of human-carrying aircraft and were known as thermal airships.
In the early 20th century, however, with developments in aerodynamics and engine technology, controlled powered flights gradually became the mainstream. By 1909, planes with characteristics that are similar to the ones we know today were established. As the years progressed, more powerful aircraft engines were developed and aircraft wiring harness innovations were applied in aerospace engineering.
Today, much like any other industry, the aircraft, and aviation sector wouldn’t be the same without the technological milestones it went through. The purpose of an aircraft wiring harness may be as elementary as any other wiring system but the way it is designed and elaborately assembled is a monument of how it has changed the course of aviation.
THE FUNCTIONALITY OF AN AIRCRAFT WIRING HARNESS
Much like how a harness works for a car, an aircraft wiring harness is responsible for signaling and transmitting electrical signals throughout the entire system. It controls system functions such as the engine, wings, landing gear, and fuselage to name a few. Typically, wire harnesses are comprised of numerous parts. For an aircraft wiring harness, there are thousands of components and miles of wires and cables that all work together to maintain the aircraft’s performance.
Manufacturers today also have to keep up with fast-evolving aircraft technologies and better aircraft wiring harnesses that can cater to new and modern features. An aircraft wiring harness not only streamlines production and the manufacturing process but also allows maintenance work to become more convenient for mechanics who need to diagnose and repair problematic aircraft. Instead of needing to individually wire and install the electrical system of an immense airplane, wire harnesses group the wires together in each specific area. If malfunctions occur and repairs need to be made, mechanics can simply diagnose and repair the specific area where there are damages.
THREE CATEGORIES OF PARTS IN AN AIRCRAFT WIRING HARNESS
The parts and components of an aircraft wiring harness are determined by the type of aircraft it will be installed in. Different factors need to be considered especially if the aircraft has to be within military standards. There are three categories of aircraft parts and they are as follows.
Standard Parts
Also called MIL-SPEC (military specification) parts, these types of components in an aircraft wiring harness are typically controlled by the military. They are usually labeled with the letter M or MS at the beginning of each number to specify that they are for military purposes. Some are also labeled with NAS at the beginning to indicate that they are of National Aerospace Standard.
Though there are other types of prefixes for standard parts, these are the two kinds that are commonly used in a military aircraft wiring harness. However, standard parts are not exclusively used by the military and are available in many aerospace sectors but the government needs to approve certain manufacturers in order for them to be deemed authorized suppliers.
Non-Standard Parts
Typically, non-standard parts are made based on standard parts but are slightly different in terms of military specification. Specifications for non-standard parts can be controlled by original equipment manufacturers (OEM).
OEMs can also designate which suppliers are authorized to manufacture non-standard parts. However, non-standard parts in an aircraft wiring harness are usually more expensive since there are only a few in the industry.
Commercial off-the-Shelf Parts (COTS)
Typically controlled by manufacturers, COTS parts are produced based on demand and marketing studies. A manufacturer can design their own parts and label them with their numbers. The manufacturer can also modify and make revisions in the design of the parts without the need to consult the government or the military.
COTS parts are also readily available for purchase in the market and are generally less expensive than the two other categories. However, since manufacturers are the sole distributors for COTS parts, they can control the price and the market. They can also freely change or modify specifications which can be inconvenient when stocks run out if replacement parts for an aircraft wiring harness are necessary.
WIRING AND CONNECTORS
Since the wiring on an aircraft wiring harness stretches for miles in length, it should be designed and organized meticulously to avoid any issues before and after production. Each design starts with a schematic that is typically designed in CAD software to help guide the assembly process.
Wires are often chosen according to the transmitted signal and electrical current required by the system. The insulation for wires also varies depending on these factors. With modern advancements, different types of insulating materials are now available depending on the requirements needed.
Wires also must have their own unique identifier to avoid any mishaps in assembly and repairs. On the other hand, when it comes to choosing a connector, three main factors have to be taken into consideration. The first one should be the number of wires the connector will attach to. The second one is the gauge of each wire and the third is the selection of wires that would go through the connector inside the aircraft wiring harness.