Guide to designing your automotive wiring harnesses
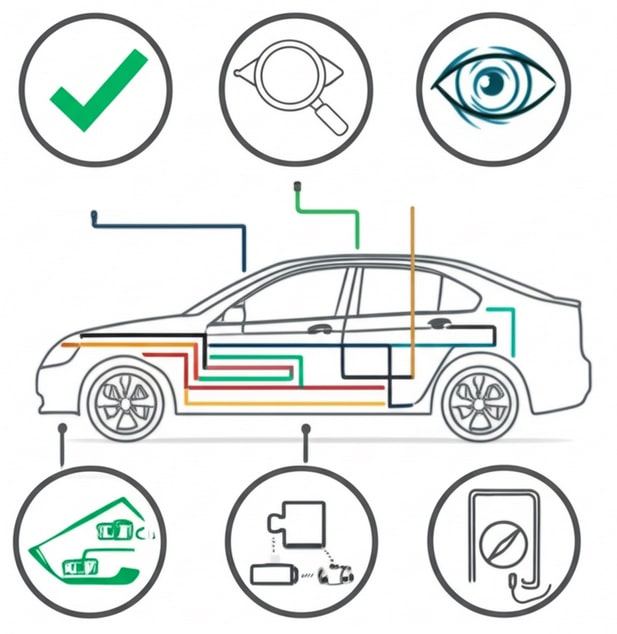
If you’re somebody who considers himself a typical car enthusiast, then you may have thought about building a custom automotive wiring harness for your car. Building custom vehicles have started to grow in popularity in recent years and it’s not unusual to see a car fanatic trying to restore or modify a specific model in their garage. For some, automotive customization does not only involve external elements but also the internal components of a vehicle. Building wire harnesses may somehow prove to be tedious and laborious but for a typical car junkie, this process may even be considered rewarding.
An automotive wiring harness consists of hundreds, if not thousands of parts. Each part is responsible for sending electrical signals throughout different components of a vehicle. This is why building your own custom harness takes a lot of time and energy. The process itself is methodical and elaborate. Focus and precision are required when it comes to assembling each component. Some people may opt to design and build the harness themselves, while others might draft a design then have it made through a manufacturer. Whichever method you choose, knowing the proper technique to design a harness and planning thoroughly before you start the building process ensures a more successful outcome.
Things to consider when designing an automotive wiring harness
Sometimes even if we thoroughly understand how something is constructed, things can still go wrong during the building process. This is why it’s essential to always look out for any possible errors or miscalculations when assembling your automotive wiring harness. Although awareness does not guarantee the elimination of design flaws, it’s still better to make changes and modifications while the assembly is still in the process rather than realizing mistakes post-production.
1) Review your design
Whether you’re designing a harness and building it yourself, or sending your schematic draft to a manufacturer, making sure that your design is up to standard is essential. When building an automotive wiring harness solely by yourself, it’s important to be extra careful and do proper research. Making changes in your design is completely normal even if you’re working with a manufacturing engineer. Since each automotive wiring harness is uniquely designed, there is no one-size-fits-all system that you can compare with yours. Each wire and cable should be measured and cut accurately according to the vehicle that it will be installed in.
It’s also important to consider the route of each wire and cable. An automotive wiring harness needs to efficiently distribute electric signals throughout the car. If the wiring system is not laid out properly, then some parts of the vehicle may suddenly stop working or even not work at all. Additionally, fastening or securing each component to the harness is essential to avoid any parts from detaching while the car is moving.
2) Avoid Materials of Low Quality
Any kind of material that is considered low quality would not last for a long time. Typically, a good-quality automotive wiring harness is expected to last as long or even surpass the life of a car. Using materials that are poorly made would not only deteriorate or corrode quickly but could also prove to be detrimental to the car as a whole. A wiring harness with faulty parts can compromise the driver’s safety when on the road so it’s necessary to do proper research regarding the best parts that are available to you.
Some materials may not be compatible with your environment and may suddenly give in when it comes to extreme temperatures. Although OEM materials are cheaper, it’s still better to invest in high-caliber components that would save you more money when it comes to repairs. However, if you’re planning to have your design fabricated by a manufacturer, it’s always best to consult the manufacturing engineer about the best options for your design.
3) Ensure proper installation
Each automotive wiring harness consists of multitudinous parts so it’s crucial to make sure that each of them is fastened or mounted properly. Since a harness handles electrical components, there is always a risk of a short circuit if not properly assembled. Crimping is also an important part of the assembly process. It is typically the method used to attach wires into terminals. If a wire is not crimped properly, there is a big possibility of faulty wiring which can lead to failures and malfunctions.
If you plan to construct the wiring harness yourself, consider soldering each crimp to reinforce the wires. When installed in a vehicle, the automotive wiring harness will be exposed to vibrations and external elements that can cause the wires to detach if not soldered. This is why doing checks and tests is very important before installing the wiring harness to a car.
4) Simplify the design
A simple design does not mean an inefficient design. An automotive wiring harness design can often be simplified without compromising its functionality. This is beneficial in terms of both the assembly process and the cost of production. Sometimes changing the location of some terminals and switches can save you a lot of money in terms of materials.
Additionally, a simple design means a more efficient and time-saving building process. This also helps avoid any confusion whether you’re constructing the harness yourself or presenting your schematic draft to a manufacturer. Considering the functionality of each part may also be helpful. If a single component can operate the same way multiple parts are supposed to, then you might want to consider the less complicated option.
5) Always perform testing
Since an automotive wiring harness should perform without any room for errors, testing is always the final step before putting your harness into action. A typical manufacturing process always requires testing before being deemed suitable for installation. As aforementioned, this is why changes and modifications are normal.
Testing wiring harnesses also includes testing the fail-safe components in each unit. The fail-safe mechanism is what protects the drivers from encountering major malfunctions once the car is on the road. Once your automotive wiring harness passes the testing process, then you can be sure that it will perform efficiently once you start driving your vehicle.